Type of Products
Moulded Rubber Products
Moulded Rubber products refer to a diverse group of vulcanized rubber products which are manufactured in a mould and the desired size and shape is obtained.
We at, Netgains Elastomer, manufacture, wide range of moulded rubber products such as ‘O’ Rings, Stripper Rings, Diaphragms, Grommets, Washers, Sleeves, Bellows, Bushings, Rubber Couplings, Suction Cups, Expansion Joints, Anti-Vibration Pad, Metal Bonded Articles, Oil Seals, Inflatable Seals, Bulb Seals, “U” Seals, “V” Seals, Endless Sealing Ring, Wiper Seals, Hydraulic Seals, Chevron Packing, etc. They are used in a wide range of applications.
Rubber Moulding Process
Compounded rubber is transferred, injected or simply put into a heated moulds, and cured to obtain required size and shape under pressure.
Factors To Be Considered in Rubber Moulding
Moulded rubber needs to maintain certain tolerance standards to produce the finished products. There are many factors which affect tolerances in the manufacturing of moulded solid rubber products. These factors are peculiar to the rubber industry and are given below:
- Shrinkage
- Mold Design
- Trim and Finish
- Inserts for Bonding
- Distortion
- Environmental Storage Conditions
- Dimension Terminology
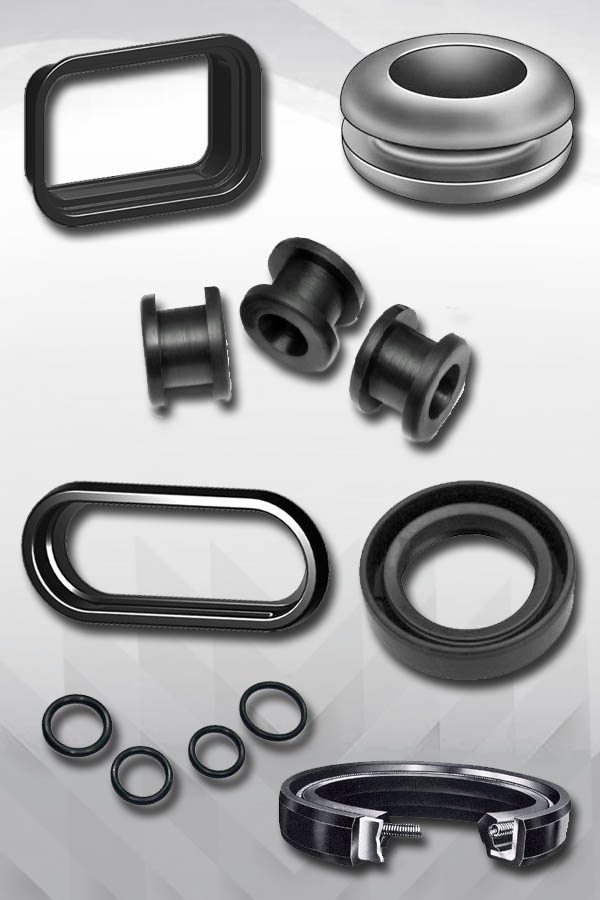
Extruded Rubber Products
A wide variety of rubber extruded products are used for various purposes, both industrial as well as commercial. Rubber is one of the most common material used in almost every industrial application. Its resilience or elasticity or flexibility makes it an effective choice for applications which involve shock absorption, sealing and fluid transportation.
We at, Netgains Elastomer, manufacture a wide range of extruded rubber products such as Extruded Rubber Profiles / Sections, Cellular Rubber Sections, Rubber Beedings, Braided Silicone Hose, ‘D’, ‘E’,’P’, ‘T’, ‘U’, ‘V’, etc. shaped Rubber Strips, Rubber Tubing’s (including transparent), Rubber Cords, Door Packing, Silicone Rubber Sleeves, etc.
Advantages of Rubber Extrusion
There are different rubber processing methods but of all the methods, extrusion remains a popular choice for many manufacturers. This is because, extruded rubber products can be produced in a neat, uniform manner. A great variety of shapes can be produced, including hollow designs for any industrial need that greatly reduce material cost and create flexible, lightweight products. Rubber materials are in great demand, making rubber extrusions and molded rubber effective ways to produce these materials.
Extruded rubber products are applied in a wide range of sealing and gasketing applications. They are available in various compounds and styles to meet specific end-use requirements involving various factors like size, tolerance, configuration, cost and performance.
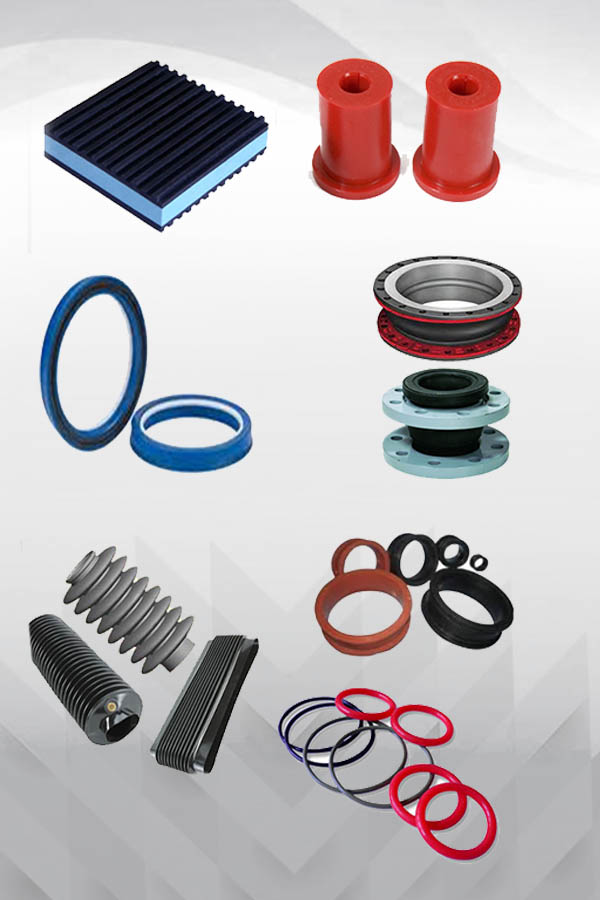
Rubber Extrusion Process
The process of extruding can be compared to squeezing of toothpaste from a tube and the paste takes the shape of the tube opening. Rubber material is processed through an extruder, during the rubber extrusion process. There are two main components of rubber extruders:
- A small heated drum: As the material enters the drum, it is softened through heating and then pressurized through the rotation of a screw and
- A die: The pressure pushes the rubber through the die, located at the end of the extruder.
Depending on the result desired, pre-heating of the material is optional. The rubber emerges from the extruder in a profile which resembles the die shape. As the possibilities of die design are nearly limitless, so also the number of possible extruded rubber profiles. After being extruded, the rubber material is cured using various methods such as salt bath, autoclave, convection, hot air, microwave and mandrel.
Methods of Rubber Extrusion- Co-Extrusion: This is considered to be a variation of the basic extrusion process. This process allows for the convergence of rubber materials that contain different properties like color and consistency.
- Cold feed extrusion: This is the process of extrusion without pre-heating. This process is best suited to produce hoses, profiles, cable and sheaths.
- Hot feed extrusion: This on the other hand is the extrusion process which involves the pre-heating before performing the extrusion process.
- Pin barrel extruders: This process performs with many pins protruding from the cylinder wall toward the screw's center and enhances the mixing and dispersing of the rubber when it is kneaded between the screws and the cylinder. This method can be applied for diverse applications.
- Vented extruders: This process has screws of an original and unique design and it is easy to maintain and occupies very little floor space.
Calendered Rubber Products
For any industrial rubber manufacturing business, calendered rubber products are the cornerstone. Calendered rubber products comprises a wide range of rubber products used in various industries, with each application having its own specific requirements. These rubber products are formed by the process of calendering.
We at, Netgains Easltomer, manufacture wide range of calendered rubber products such as Rubber Sheets, Rubber Mats, Anti-Skid Sheets, etc.
What is Calendered Rubber?
Rubber that is formed by using a method known as calendering is known as calendered rubber. Such type of rubber is used to produce different products like rubber sheets, rubberized fabric, elastomeric films etc. Calendering is a mechanical process in which rubber or plastic is pressed. It is a finishing process which is applied to textiles and paper. During the process, fabric and rubber or plastic material pass through heated rollers to flatten, smooth and commingle the two or more materials and give a shiny, flat and smooth surface. The final surface characteristics depend on the pressure exerted by the rollers, on their composition, temperature, surface designs, type of coating or glaze initially applied to the material to be calendered. After the calendering process the material is then wound into rolls and placed into storage.
Byproducts of Calendered Rubber
Although there are several calendered rubber products, there are two main products which are widely produced and widely used. They are as follows:
- Rubber Sheets: A very common product formed out of the calendering process is calendered rubber sheets. They can have multiple layers of both the elastomeric and polymer "combined" together.
- Rubberized Fabric: Rubberized fabric formed from calendering is smoothed, glazed, polished, or given a embossed surface, depending on its use.
Types of Compounds Used
Elastomers that can be used for calendering include:
|
|
Fabric Materials
Fabric that can be used for calendering include:
|
|
Metal Bonded Rubber Products
Rubber to metal bonding is defined as a process covering a number of interdependent processes, in which rubber is adhered to metal substrate. Today, various factors concerning environment have an impact on all aspects of commerce and industry. Rubber to metal bonding is no exception and the process is undergoing changes to reflect these concerns. Because of the several parts used today consisting of bonded rubber to metal, there are various custom shops who specialize in the manufacturing of these parts and they work with customers from the design level through production.
We at, Netgains Elastomer, manufacture wide range of metal bonded products such as Rubber Rollers, Rubber Seals, Rubber Expansion Joints, etc.
Rubber Bonding Process
The rubber can be moulded to a metal piece. It can also be adhered to a metal piece.
The rubber to metal bonding process involves three elements:
- Rubber
- The bonding agent
- The substrate
Any type of rubber can be used but usually the selection of the polymer base and its related compound depends on the product specification. The condition is that the rubber should easily flow into the mould without developing a significant level of cross-linking, and thereby a bond can be created using any rubber compound. It is also advised to avoid substances that will bleed rapidly to the surface of the uncured stock. Before the moulding takes place, the metal is made completely free from rust and other impurities by degreasing, sandblasting or shot blasting. The bonding agents comprises polymer/solvent solutions, having a primer coat related to phenolic-style resins and a topcoat of polymers and other materials. Usually the solutions used are patented. The substrate used depends on the strength and durability requirements of the application.
Science Behind the Rubber to Metal Bonding Process
The science behind this process is very complex as well as varied. Often the type of rubber or polymer used depends on what type of metal is used and the part that is to be manufactured. Determining the appropriate bonding agent is very important. The selection process depends on three factors:
- Rubber to be used
- The elasticity of the rubber
- The component design
Originally, the metal used was steel in all its forms and grades. Steel is still in use but increasing use is also made of aluminum alloys and polyamides. Any material can be bonded to rubber, the only condition is that that it can bear the heat and pressures of the rubber moulding process. However, the results of bonding rubber to alloys, like brass, bronze depend a lot on the composition of the alloys.
Applications of Rubber to Metal Bonding Units
The products made from the bonding of rubber to metal are used in various areas of the medical, commercial and industrial fields. Many of the products are used for the isolation of vibration and noise in manufacturing applications, including automotive and engineering applications. Larger sized pieces are used to decouple translational movement for bridges and buildings.
There are various products made out of the rubber to metal bonding process such as:
- Gaskets: Gaskets are a type of seal made often with bonded to metal rubber.
- O-rings: These rings to seal rotating or sliding shafts are often made with a rubber coating on metal, are used widely in applications like shock absorbers and differentials.
- Piping:Piping is often bonded with rubber when the pipe line is required to be vibration absorbent and more insulated.
- Press bonding:This refers to a non-heat or chemical process of bonding rubber to metal, involving the bonding of a preformed rubber piece onto metal piece by a predetermined groove or space and a mild adhesive agent.
- Rubber rollers: Used to squeeze water out of pulp in paper manufacturing, the roll has a metal core lined with rubber to perform efficiently.
- Seals: Often used as shut off pieces in hydraulic equipment, seals are the most common types of products formed with rubber bonding technology.